1 概述
我厂为新型干法水泥厂,生料制备系统共用4台Φ3.5m×10m中卸式烘干生料磨与2条2000t/d的水泥生产线相配套。试生产2年来,磨机年均台时产量一直未达到设计能力,水泥窑经常因生料短缺而停产;而且生产中磨机研磨体“窜仓”(在隔仓篦板完好的情况下)、“饱磨”等不良现象也时有发生。经过我们在生产实践中的摸索,对研磨体装载量和级配进行了调整,不仅避免了上述不良现象,而且取得了增产降耗的显著效果,见表1。
表1 磨机改进前后与设计各项指标的比较
项目 |
台时产量(t/h) |
运转率(%) |
电耗(kWh/t) |
球耗 |
生料磨 |
系统 |
(g/t) |
设计 |
75 |
70 |
16 |
26 |
- |
改前 |
63.09 |
40.82 |
20.00 |
30.80 |
60 |
改后 |
75.38 |
53.01 |
15.01 |
25.00 |
45 |
效果 |
+12.29 |
+12.19 |
-4.99 |
-5.80 |
-15 |
比较(%) |
+19.5 |
+29.9 |
-25.0 |
-18.8 |
-25.0 |
2 磨机产量低的原因分析
试生产阶段,我们按照磨机原设计的研磨体装载量和级配(见表3)装球,发现球在磨内的装载高度Ha,几乎与双层隔仓篦板(即粗磨仓与烘干仓之间的篦板)的高度H一致,二者的高度差仅为50mm,如图所示。
原料磨运转时,粗磨仓的研磨体极易从卸料锥中间通风孔(Φ540mm)以及卸料锥和篦板内圈(Φ1160mm)之间的进料空间中窜至烘干仓。其原因为:
①由于H与Ha之间的高度差较小,磨机运转中,研磨体受到“碰撞”、“挤压”后,运动轨迹发生改变而“窜仓”
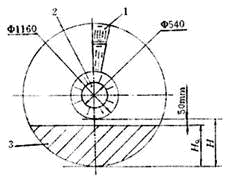
粗磨仓断面示意图
1.双层隔仓篦板(32块);2.卸料锥;3.研磨体
②隔仓板附近的研磨体发生“轴向窜动”的机会较多。因为隔仓板附近的研磨体受到衬板和隔仓板“双重带球”作用,而中间部分的研磨体受到的带球作用一定要低于隔仓板附近的研磨体。由于受到的作用力不同,二者被带起的高度也不一样,隔仓板附近的研磨体被带起的高度要高。运转中此处的球面将出现凹坑,其它处的研磨体受到“挤压”作用后,将向凹坑处移动,故极易发生“窜仓”。
研磨体“窜仓”后,造成级配失调,粉磨效率降低,产量下降,严重时导致“饱磨”。
另外,磨机在生产条件正常时,其台时产量也仅能在60~70t/h的范围波动。在这种情况下,我们对出磨物料细度作了测定,见表2
磨别 |
1号 |
2号 |
3号 |
4号 |
台时产量(t/h) |
58 |
69 |
58 |
64 |
细度(%,0.08mm方孔筛筛余) |
30 |
35 |
25 |
29 |
根据我国大中型水泥厂的生产经验,一般一级闭路圈流系统控制出原料磨磨物料的细度为30%~45%的范围之内,相比之下,我厂出磨物料细度太细。于是我们采取了降低磨内研磨体装载量的措施,同时对级配进行调整。
3 改变磨内研磨体的装载量和级配
为了不影响生产,首先在两个系统的各一台磨上进行试验。将磨机装载量由原设计的100%负荷改为90%;同时,为了增加研磨体与物料的接触面积,将粗磨仓原设计研磨体的级配作适当调整,降低了钢球平均球径,见表3。
研磨体尺寸
(mm) |
研磨体装载量(t) |
粗磨仓 |
细磨仓 |
设计 |
改进后 |
设计 |
改进后 |
Φ90 |
10 |
8 |
- |
- |
Φ80 |
12 |
9.5 |
- |
- |
Φ70 |
8 |
9 |
- |
- |
Φ60 |
8 |
7.7 |
- |
- |
Φ50 |
3 |
2.7 |
8 |
7.2 |
Φ40 |
- |
- |
17 |
15.3 |
Φ30 |
- |
- |
14 |
12.6 |
合计 |
41 |
36.9 |
39 |
35.1 |
填充率(%) |
27.5 |
24.8 |
27.5 |
24.2 |
平均球径(mm) |
74.4 |
73.4 |
38.5 |
38.5 |
改进后,磨内Ha-H的高度差由原来的50mm增至150mm。通过试运转两个月,磨机增产效果显著,两台磨月均台时产量全部达到设计能力75t/h以上,避免了研磨体的“窜仓”现象。随后,我们在另外两台磨上也作了改进。
4 注意事项
4.1 严格控制入磨物料的粒度
原料磨入磨物料粒度的大小是影响磨机产量的主要因素。若入磨粒度较大,粗磨仓必须加入较多的大球才能击碎物料。我们将研磨体装载量和级配改变后,粗磨仓钢球的平均球径恰恰变小。为不影响粉磨效率,我厂将入磨物料粒度严格控制在>25mm的物料筛余小于10%;同时,在工艺操作上保证喂料的稳定。
4.2 及时调整研磨体装载量和级配
原料磨磨机在生产一段时间后,研磨体会逐渐磨耗,因而改变了原来的装载量和级配的比例,如不及时添加新的研磨体,就会降低粉磨效率,降低产品的质量和产量。特别是装载量改为原设计的90%负荷以后,尤其应注意制订合理的补球制度。我厂为保证磨机在正常的研磨体装载量和级配下运转,制订了如下措施:
①研磨体的磨耗不能超过现装载量的5%~7%。
②磨机运行5~10个月后,必须进行一次清仓配球。
为了不因停磨补球影响原料磨产量,我们充分抓住磨机定期检修的机会进行研磨体的补充。从而也提高了设备的运转率。
5 改进后的经济效益
由表1可见,磨机改进后,单机年均台时产量增加12.29t,原料磨及系统的电耗都低于设计指标,并优于国家建材局水泥厂节能规定的干法生料磨电耗17.5kWh/t、系统电耗26kWh/t的指标。如果按照年平均生产150万t生料计算,系统全年节电约870万kWh,节约电费约260万元;节约钢球用量54.5t,节约资金达32.7万元(按6000元/t)。这里尚没有考虑磨机增产带来的效益,单就能耗创造的经济效益就已经十分可观。
我公司所产的磨机有:球磨机,水泥球磨机,熟料球磨机,节能球磨机,也可根据客户要求相应加工,及相应配件
电话:+86-0371-63759558/67878896/67878986
|